The European Union is concerned that industry 4.0, the digitalisation and automation of industry, may lead us away from the sorts of societies and industries that we want and need to build. Industry 5.0, where we need to get to, encapsulates the concepts of human-centricity, resilience, and sustainability.
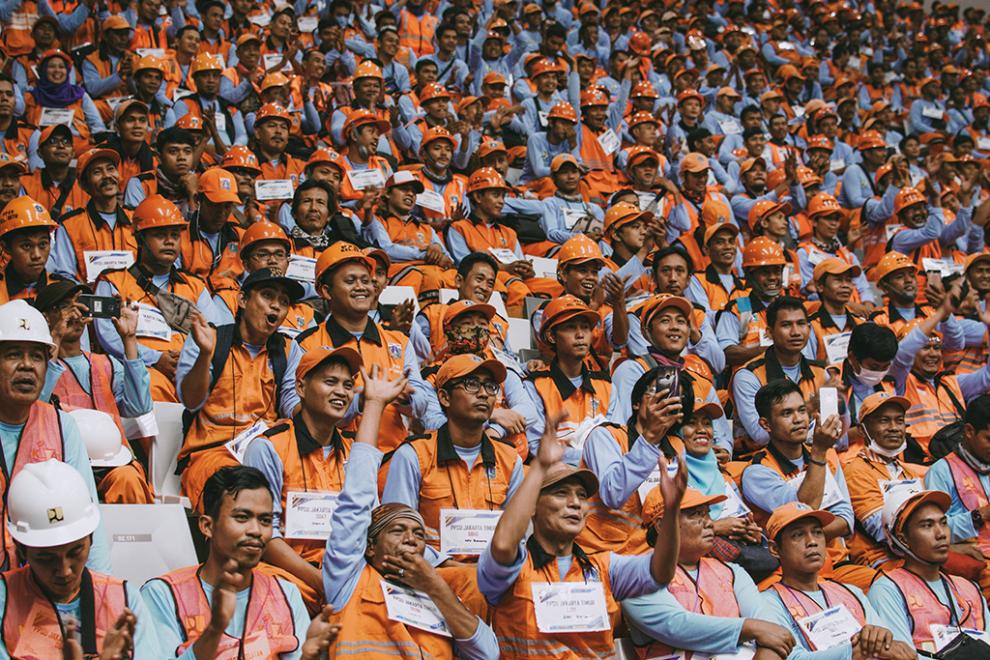
Industry 4.0, if left unrestrained, it is feared, threatens environmentally ruinous directions in economic growth, unstable supply chains, joblessness and the immiseration of work. How we get to industry 5.0 is another question.
At the heart of the whether industry 4.0 leads us toward or away from a cleaner fairer industrial system lies, we believe, is 'managerial intent': the diffused and uncoordinated decisions made by millions of managers around purchasing and implementing new technologies. One crucial decision that managers make, for example, is between technology that automates – or replaces workers - and augmentation – technology that keeps workers in place and instead improves or sustains their productivity. Augmentation is the choice that is in-keeping with what has been termed human-centricity – a core value of industry 5.0.
Technology adoption decisions are strategic decisions of course – but they are also, as we have been discovering, not just 'rational-economic' but also values-based decisions. Not all owners and managers want to get rid of their workers – even if they can. For example, we are finding that firms we initially expected to be fully committed to full automation (think factories devoid of human life) – are in fact committed to putting the human first and have in place policies that dictate not introducing technologies that disadvantage workers. Having said this, we are also finding artisanal craft-based firms, who we anticipated would be examples of putting the skilled human first, are in fact fully committed to automation. Values, not raw economic rationalism, explains these decisions.This suggests that changes of direction and different choices about what technology is for, are possible, even within the existing economic system.
Industry 4.0 can be characterised as both a particular managerial mindset and economic model. Within the industry 4.0 mindset, digital technology feeds managerial aims of acceleration and escalation – as Hartmut Rosa puts it. Within this mind-set workers are regarded as a problem – as a potential threat to production and as constituting a 'wage bill problem'. This is probably the economic scenario we are most familiar with: this is the rationalistic, shareholder-driven, profit-focused epoch of late industrial modernity. Because workers are seen as a threat, they are controlled and surveilled and given limited, and ideally no, voice in firm decisions. And it is this version of how to do business that is generally promoted and supported by government in most western economies.
This mind set also gives rise to a particular type of demand for technology – and we see this in high demand for automation (not augmentation), surveillance technologies aimed at controlling workers and co-bots that transpire to be an intermediary step towards replacement automation. For good reason, workers are suspicious of such technologies.
Industry 5.0, by contrast, is a managerial mind-set and economic model in which workers are viewed very differently. In this scenario workers are trusted and involved in decision making – this model can still be found to a greater extent in Sweden and Germany than it can be in Britain or the US, though not consistently. But strangely, this is in fact an old not new economic model. It is the model, and we have chosen our terminology very carefully, of shared prosperity - the model that emerged after the Second World War in the US, Sweden, Germany and elsewhere. Even Britain dabbled in it as it built welfare capitalism. It involves government support for fairness, worker's rights, and collectivity. Because it involves a strong and direct role for government (the early post-war US government directly intervened in strikes, supporting workers!) it is also model that can encapsulate sustainability. Robert Kennedy, for example, was able to talk about shared prosperity and respecting the limits to growth – the physical limits of the planet - in the same speech. So, in a sense, Industry 5.0 is a form a rational-nostalgia, an attempt to find our way back to a better, fairer, more managed way of organising the economy.
Critically, in this model, workers are fully involved in decision-making about technology investments and are able to secure a better share of any resulting productivity. They have genuine power through collective organisation – and we are talking here about unions.
Also in this model, in this mind set, demand for very different styles of technology is apparent. Augmentation is favoured over automation. Surveillance is avoided, not only because workers don't like it (and may simply refuse to work under its panopticon gaze) but also because they are trusted to get on with their work. Data collection is used to support workers on the shop floor. Managers can step back because workers generally know what they are doing. Co-bots are just that, they are there to serve workers – make their work easier and safer where it is needed and wanted.
The idea that unionised workers reduce productivity is deeply embedded in our thinking – but wholly incorrect. For example, comparison of productivity levels between the Netherlands and Belgium shows a positive effect of Unionisation on productivity. Belgium and the Netherlands score high on the Digital Economy Society Index (DESI). However, the 'average' Belgian worker presently delivers 25.000 euros more yearly than a Dutch worker does. Unionisation rates in Belgium are at up to 50% of workers. In the Netherlands, it is around only 10-15%. Over the past two decades, the Netherlands has been seen as a 'labour market participation' hero. This high participation rate has only been achieved by allowing workers to work part-time. That is, of course, a good thing. However, if compared to the Belgian situation, when working hours are taken into account, the Belgians have the same labour market participation rate as the Dutch do, while the productivity rate delivered through this participation is, as noted, much higher in Belgium. It seems that pressure from trade unions in Belgium helps firms make choices towards more productive solutions and better use of technology - not least by ensuring that workers are up-skilled and ready to use them.
However, we cannot simply leave it to managers to ensure worker engagement – engagement cannot be at their largesse. We need to move, in other words, on from 'soft models' of worker engagement and ensure that workers have real power, that can balance that of shareholders, owners and managers. Workers, in other words, need a real voice in co-designing technologies, implementation, and in the use of technologies.
With a new technology wave upon us in the form of AI and global warming threatening to collapse our civilisations, we need those workers in the board room with real power at their disposal, representing the interests of society at large. They will press their own interests, yes – but also those of their neighbour’s and children. Unions gave us the original shared prosperity, let them now also help us save our civilisations. That is the mission of industry 5.0. and this is certainly one way of getting there.
Written by Professor Chris Ivory – Up-Skill Project and Professor Steven Dhondt – Bridges 5.0 Project.