A paradigm shift from automation to human-machine augmentation
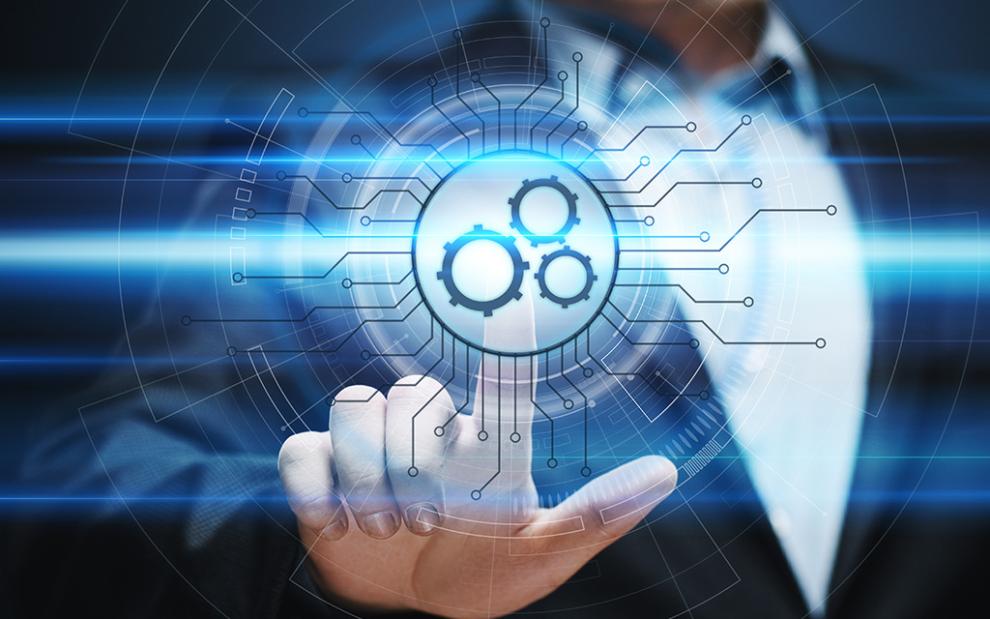
The 4th Industrial Revolution (Industry 4.0) is the implementation of autonomous robots and digital technologies, such as AI, big data and analytics, cloud computing, the Internet of Things and augmented reality, within the industrial and manufacturing sectors.
These technologies create a system whereby machines in factories are wirelessly connected and use sensors to monitor and map entire production processes, and make autonomous decisions based upon the data received from other parts of the system, or from external sources such as customer orders or raw material supply and logistics data. Wireless connectivity and the augmentation of machines will provide faster response times through real time communication between systems, which will reduce production costs, improve the consistency of product quality, and allow for mass customisation.
In addition, these digital technologies can create virtual versions of real-world installations, processes and applications (digital twin technologies), allowing for testing and analysis to make cost-effective decentralised decisions prior to real world installation. The information gathered from these virtual copies can then be implemented in the real world and linked via the internet of things, allowing for cyber-physical systems to communicate and cooperate with each other and human staff to create a connected real time data exchange and automation process for Industry 4.0 manufacturing.
The 4th Industrial Revolution not only promises more efficient production processes and the ability to mass produce customised products, but also to reduce waste, energy consumption and improve working conditions. However, primarily, Industry 4.0 is being driven by technology developers and the companies that will utilise them, with the bottom-line goal of increased profits. And, therefore, there are concerns that these new technologies could cause widespread societal and organisational damage through unemployment, lost skills and lost opportunities in innovation and quality.
Industry 5.0 addresses these challenges by placing the goals of the emerging technologies beyond solely being an enhancement to productivity and efficiency, to within the broader context of societal well-being and environmental protection and places the worker at the centre of the production process. Technological and industrial development will bring widespread societal and environmental benefits if channelled and managed correctly, dispelling the narratives that technology will either be the solution to all our problems, or a potentially destructive power wielded by elites. Ultimately, it is up to us how, where and when technology is utilised, and these are some of the primary concerns of Industry 5.0 and the Up-Skill project.
Industry 5.0 broadens the objectives of the new technologies and questions their efficacy in relation to workers, industry, society and environment. It does not question whether the emerging technologies should be implemented, as it is widely understood that the proliferation of automated robots and digitally connected manufacturing systems is inevitable. But rather, how they should be implemented and to what end? And this is what the Up-Skill project, in part, is seeking to understand within a range of industrial, manufacturing and supply chain settings.
In some cases, this could mean full automation, and in other cases it could mean the implementation of technologies that improves the ability of engineers, skilled artisans and craftspeople to do their work. Whatever the case, understanding the most valuable way to integrate these new technologies for all concerned, will help ensure their efficient implementation, reducing errors and over automation, and provide a sustainable, profitable and equitable framework for industrial development in Europe.
Sources:
What is Industry 4.0? How Does it Work? (A Beginners Guide) - TWI (twi-global.com)
Industry 5.0 (europa.eu)