The Up-Skill project aims to explore the intricate relationship between automation, skilled labour, and organisational systems within the context of Industry 5.0. This article delves into the depths of the project's objectives, methodologies, and anticipated outcomes, shedding light on the critical role of enabling technologies in shaping the future of manufacturing.
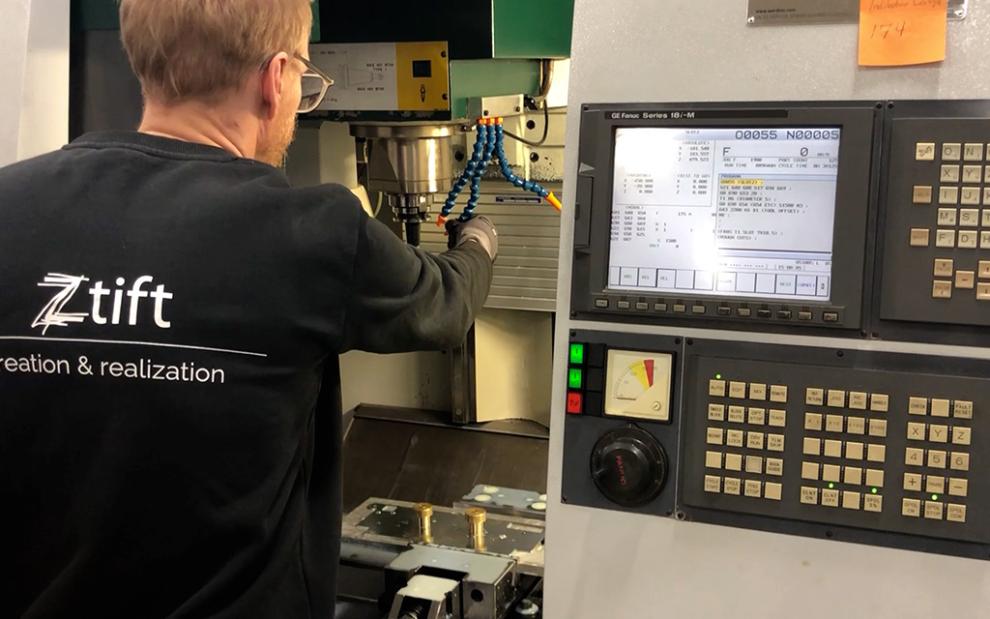
TWI recently published a report entitled “Installed Hardware for Trial Manufacture.” The focal point of this report is to delve into the enabling technologies identified for each participating company, following on from the Best Practice Technology Solutions report published by Lancaster University. With a foundation based on real-world manufacturing challenges at the Up-Skill case study locations, the report provides insights into the current technological landscape, the planned solutions aimed at addressing these challenges, and the identification of specific hardware and processes crucial for implementing new technologies across various case studies.
The comprehensive case studies featured in the report employ a diverse range of methodologies, including hardware investigations, software data mining, and reviews of existing commercial hardware. Each study meticulously considers manufacturing processes and managerial intent, aiming to streamline outdated procedures, leverage improved technologies for enhanced efficiency, and explore opportunities for data-driven enhancements in product yield and performance.
For each participating company, the report systematically examines various aspects, including business area definition, identified issues, current processes, and planned solutions. Moreover, it outlines hardware, software, infrastructure, and training requirements, along with assessing environmental impacts and associated risks and opportunities.
Ztift , a company based in Eskilstuna, Sweden, manufactures a variety of products and components, particularly door locks and their related mechanisms, for household, marine and security system applications, which are typically low volume, high quality items that require a high degree of assembly by hand and a significant amount of skill and experience. These skills and years of experience are difficult to pass on to newer members of staff.
It is important for firms to ensure that production skills remain consistent over time and any technology that facilitates the capture and flow of information to the workforce should be considered a worthwhile long-term investment. Therefore, after consultation with Up-Skill partners, Ztift have installed computer numerical control (CNC) milling and lathe machines. These machines will not only improve the conformity and quality of the products and reduce waste, but also allow for the collection of data for analysis and improvements to performance.
In addition, the team at Ztift are experimenting with augmented reality (AR) technology to assist workers with lock assembly. Up-Skill partner Mälardalen Industrial Technology Center have created 3D images of the lock components and mapped out each step of the assembly process with instructions. This allows workers to view the components, process steps and instructions on their 3D headsets whilst simultaneously assembling the physical lock components. The aim of the AR system is to train new employees on general lock assembly, and provide more experienced employees with a resource for assisting with specific procedures for a variety of locks, thereby helping to remove obstacles to work rotation.
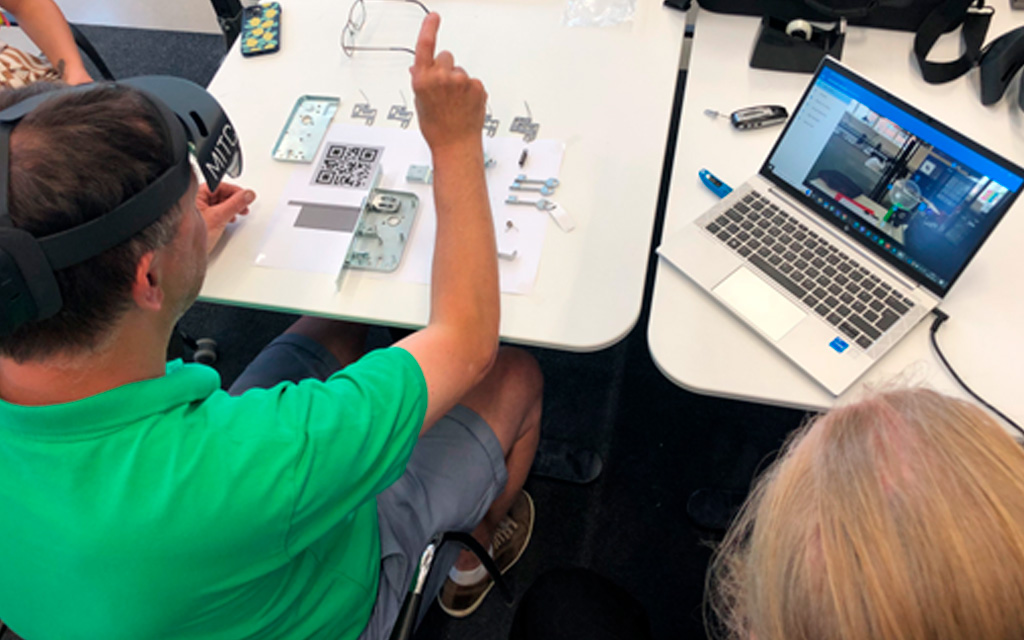
The AR technology and CNC machines will lead to greater fluidity of knowledge and job roles throughout the entire production workforce, mitigating the risk of Ztift losing a specific skillset due to retirement, and potentially creating greater job satisfaction due to the more varied nature of work on the shop floor.
These more nuanced considerations of technological implementation are something that the ethnographers from the case study locations will be very interested in, hoping to understand how technologies affect workers´ attitudes, job roles and creativity so any negative effects can be mitigated, and positive ones enhanced.